In the 56 operations, the thermal control equipment itself (software and hardware) caused the action 9 times, accounting for 16.1%; 6 measurements occurred due to a failure of the thermal control measurement element, accounting for 10.7%; maintenance is not in place Caused the action 2 times, accounted for 3.6%; The action caused by the mechanic reason was 26 times, accounted for 46.4%; The action caused by the electric reason was 7 times, accounted for 12.5%; The reason is unknown 6 times, accounted for 10.7%. Figure 1 shows the distribution and change trends of the action of the thermal protection system in Shanghai's power system from 1998 to 2001.
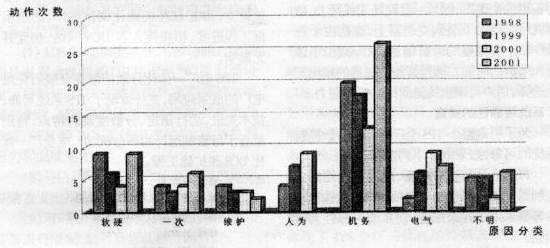
2. Thermal protection system reliability analysis
In 2001, the Shanghai Power Grid thermal control professional did a lot of work to improve the reliability of the thermal protection system and reduce the number of protection actions. It constantly improved and improved the control logic and system configuration, and performed the cold and hot test and acceptance of the protection system. The use of high-quality primary measuring components, especially during the summer peaking and APEC meetings, is even more meticulous in doing a good job of inspection and maintenance, which has played a very good role. The following is a combination of the protection action conditions, on the thermal protection system reliability analysis as follows. 
2.1 Thermal Control Software and Hardware Faults
Software and hardware failures caused protection actions 9 times. One of the actions caused by the status power switch tripping, the bearing vibration protection preamplifier failure and the Simadyn-D power supply module failure caused two actions each time, the DPU board fault caused one action, the BMS control card was burned out and the BMS input terminal board fuse Each action caused by a knockout occurs 1 time, and the configuration software error causes the action to occur once. In these nine actions, the fuse blowout of the BMS input terminal board is a design issue and has been rectified. The preamplifier failure and the Simadyn-D power supply module failure are the same set of DCSs in the same power plant. Since the DCS was put into operation Many problems have been exposed and many preventive measures have been taken. However, much work remains to be done to further enhance its reliability. 
2.2 Thermal Control One-time Measurement Component Failure
The protective action is caused 6 times due to a failure of the thermal measuring primary measuring element. One of the primary pump outlet pressures caused a failure of the primary measuring element, and the turbine's “lower oil level in the fuel tank†caused the signal to be actuated 1 time by mistake, and the induced draft fan's actuator malfunction caused 1 action. The control air source caused the water to lead to water supply. The misoperation caused by door adjustment caused the action to occur one time. The metal temperature protection system of the bearing mistakenly made the action of “high temperature of the turbine bearing metal†once. A large number of injection surfaces of the Moog valve of the small-sized machine caused the EH oil pressure to cause the action to occur once. Wherein the control of the gas source with water, if it is possible to periodically drain the compressed air line, it is completely avoided, and the Moog valve injection is caused by the fact that the replacement of the Spare Parts of different manufacturers during the inspection process did not check the match. 
2.3 Improper maintenance
Improper maintenance caused the action 2 times. The actions of the gas source pipeline for control are caused by the pressure drop of the air source caused by freezing. The overspeed probe cable wears and causes signal grounding to cause the action once. From the action point of view, as long as the daily maintenance work is done finer and deeper, these two actions can be avoided. 
2.4 Human Factors
In 2001, the plant strengthened the management of the actions caused by 9 human factors that occurred in 2000, and carefully implemented the rules and regulations in the troubleshooting, routine tests, operation and operations, effectively eliminating the actions caused by human factors. To a very good result. 
2.5 Reasons for the mechanics The actions caused by the reasons of mechanics accounted for 26 times, accounting for 46.4% of all actions. The coke failure caused the action 5 times, the furnace negative pressure caused the operation 4 times, the coal feeder blocked the coal and caused the furnace flame to lose the action 2 times. During the routine test of the electric pump, the coal feeder power supply voltage was low 2 times and the door was shaken. Action 7 times, caused by operation inadvertently caused the water level fluctuation of the drum to increase and caused the action twice. The welding port of the condenser was broken and the action caused by the low vacuum was performed 1 time. The joint of the fuel valve oil pipe fell off and caused the action 1 time. The fuel pipeline servo valve The stuck-together causes the fuel to be interrupted and the heavy oil pressure caused by the performance test to cause a shutdown each time. A considerable part of the reasons for the mechanics related to the operator's experience, proficiency, etc., also relates to the timely transformation of equipment problems, the timing of routine testing and the implementation of the pilot program, which requires coordination and attention of all parties concerned. . 
2.6 Electrical causes Electrical causes 7 movements. The actions of the three-phase contactor of the vacuum pump A are caused by the stuck one-time operation; the jump-off machine is caused by the jump-change main transformer A (the protective platen is not removed) once; the tripping of the excitation system control module causes the tripping machine; electrical Failure to pull the DC power supply when checking the fault causes the coal feeder to lose power and shut down the furnace 1 time; in the electrical test, the 1lOV power supply enters the MFSS and burns out its card to cause the shutdown; the horizontal protection action of the 220kY main transformer switch trips and the unit MFT moves. 1 time; loss of 110V DC power supply causes thermal protection. The loss of power to the on-site protective equipment causes the unit MFT to act once. In these 7 out of 3 occasions, if the electrician can earnestly implement the rules and regulations, removing the protective pressure plate and doing a good job of monitoring and quarantine measures can be completely avoided. 
2.7 Unexplained Causes
The reason is unknown 6 times. Unexplained reasons are mainly due to incomplete accident records. Some signals that should be entered into the accident records are not accessible due to the limited number of design points. As a result, the actions cannot be analyzed and found based on the accident records. On the other hand, the operating personnel do not carefully monitor the disc and the actions cannot be correct after the operation. The flow of information describing the changes in equipment operating parameters before and after the operation adds difficulty to the analysis of the causes. Second, the operating personnel did not faithfully reflect the situation, which was also the factor that led to the analysis of the causes. 
From the above analysis, it can be seen that some actions can be avoided by reforming, strengthening maintenance and inspections, strengthening basic management, and correct judgment and handling by operators. For unclear actions, it is not difficult to find out the reasons for setting up the necessary monitoring measures according to the degree of importance, grasping the equipment operating status, and accurately describing the information flow before and after the action. 
3, improve the thermal protection system reliability recommendations As the power generation equipment gradually tends to large-scale, the number of failures also increased in an exponential manner, which led to a corresponding increase in the type and severity of failure consequences. In order to eliminate (or at least reduce) the consequences of failure, a large number of automatic protection systems have to be used in order to:
(1) Attract operator attention to abnormal conditions (warning lights and alarms);
(2) In the event of some failure that may cause serious consequences, stop the equipment;
(3) Elimination or mitigation of abnormal conditions caused by failures, otherwise it will cause more serious damage;
(4) To replace the function that has expired;
(5) Prevent dangerous situations in important positions. 
Therefore, how to improve the reliability of the protection system is a very important task. In the following, the author combines thermal monitoring and technical supervision practices to express some opinions on how to improve the reliability of thermal protection systems. 
3.1 General Considerations
The goal of setting up a thermal protection system is to minimize the severity and extent of the various faults and disturbances from the system equipment and the possible damage to the system equipment. Therefore:
(1) The setting of the protection system must avoid the use of the same component for two sets of devices in order to reduce the possibility of simultaneous failure of two sets of devices due to a single accident;
(2) The components used in the protection system shall have a proven quality in order to ensure that the reliability of the protection system is not reduced by unknown or unproven components;
(3) The setting of the protection system shall minimize the possibility of component failure or misoperation. This possibility is due to external influences such as electrical transients, electromagnetic interference, vibration, shock and temperature;
(4) The arrangement of the protection system should be carefully designed to minimize the possibility of human error caused by misoperation;
(5) When consciously prolonging the removal time, carefully consider:
- Impact on the stable operation of system equipment or reduce the stability margin;
- It may cause or increase the degree of damage to the equipment and thus extend the maintenance time and downtime. 
Careful assessment of the economic losses caused by misoperation. For those protection functions that will seriously affect the safety of the equipment, rectification should be based on improving reliability. The protection function that has little effect on the safe operation and the technical and economical nature is poorly demonstrated may be considered as an alarm or cancelled after repeated argumentation. 
3.2 Keep the system as simple as possible while satisfying functional requirements.
"The simpler the more reliable," is the most important theorem of reliability engineering. Therefore, one of the steps to improve the reliability of the thermal protection system is to simplify the system and its circuit as much as possible on the basis of meeting the safety requirements of the equipment. This can effectively reduce the number of components used and reduce the risk of failure. No matter how high the reliability of each component or component and the number is, the reliability of the system will be reduced. Because, electronic components have a problem of lifetime and accidental failure probability. According to information, in a complex system, 5% to 10% of components are completely redundant, but when these components fail, it is still possible to interrupt the operation of the equipment and remove these redundant components, not only the amount of maintenance and funds Decline, and it will lead to increased reliability. Therefore, under the premise of meeting the functional requirements of the system, it is necessary to keep the system as simple as possible, unnecessary components and redundant complex structures, and only increase the probability of failure of the system. 
3.3 As far as possible, mature technologies and standardized components are used to “maturity and stabilityâ€. This is another important theorem of reliability. As we all know, electronic components constitute the basis of the control system, there is no reliable components, and then the perfect design, it is difficult to make the system and equipment to achieve the desired goals. Therefore, mature technologies and standardized components should be used as far as possible. Although this will sacrifice some advanced features, it will ensure reliability. For example, the US “Rover†heart that left the Earth to Mars in December 1996—the CPU is Intel’s 80C85 developed in the 1970s, not the Pentium series CPUs that had been successfully used at the time. This is because the more complicated the circuit equipment is, the more sensitive it is to outside interference, and the more rigorous and careful preventive measures need to be taken.
To this end, as far as possible to grasp the failure mechanism of various components and failure modes, to understand its reliability data, which is conducive to quickly analyze the failure mechanism in the future, grasp the component selection criteria, provide a basis for design improvements, in order to take the appropriate early Preventive measures to continuously improve the reliability of the protection system. 
3.4 Strictly Controlling the Environmental Conditions of the Electronic Room
Environmental conditions include temperature, humidity, cleanliness, vibration, and electromagnetic interference. The same device has different reliability under different working and environmental conditions. In bad conditions, the equipment is prone to failure or failure. For example, when the resistance and capacitance increase 10°C per temperature, the failure rate increases about twice. The failure rate when this component is operated at a high temperature of 125°C is 32 times the failure rate at 25°C. Therefore, we must strictly control the environmental conditions in the electronic room and the control room in accordance with the requirements of the regulations, and prohibit the arbitrariness of irrelevant personnel. This will not only extend the life of electronic devices, but also improve the system's operational reliability. 
3.5 Regular Maintenance Improves the Reliability of Connectors
Try not to use plug and socket connections. The connector is an important device for controlling the signal connection. The proper connection is not only reliable, easy to operate, safe and reliable, but improper use or over time will cause or cause problems such as poor contact, falling off, and corrosion. Especially in places with high vibrations, relative movement between the plug and the socket may occur, and this movement combined with other environmental stresses may cause wear and corrosion, resulting in wear debris and considerable changes in contact resistance. Therefore, as far as possible not to use the plug, socket connection, where the connector must be used should pay attention to:
1) When a small number of multi-core plugs can be used, it is absolutely necessary not to use a large number of low-core plugs;
2) In order to prevent loosening, self-locking structures should be used as far as possible, without using wire ties;
3) Directional connectors must be used and the extended guide ring prevents damage to the pins;
4) Must be regularly checked and maintained;
3.6 Early Detection of Failures Using Condition-Based Maintenance Technology
Failure is an unexpected state of equipment. In this state, the equipment performance is obviously lower than its normal level, and it is difficult to complete the predetermined function. If the equipment continues to be in such a state and cannot be processed in time, it may evolve into an accident resulting in safety and environmental consequences. However, no matter what measures are taken to improve the reliability of the equipment, faults always occur. Therefore, early detection of failures can increase the availability of equipment, and rapid and correct maintenance measures can reduce the average repair time and increase the average time between failures. 
A large number of failures indicate that equipment failures will not occur instantaneously and will always experience a period of development. At some point during the development of the fault, it is possible to detect the point at which the fault is occurring or is about to occur, which is called a potential fault point. Figure 2 shows the general process of the occurrence of a potential failure (called P-F diagram), which shows the point where the failure started and deteriorated until the failure can be detected (potential failure point "P"), and if not detected, it is not corrected. , performance continues to deteriorate - speed will often become faster until it reaches the point of functional failure ("F"). 
If a potential fault is detected between points P and F, there are two possibilities: First, prevent and reduce functional failure. In this case, repairs can be performed before the existing components are completely inoperative, which can prevent malfunctions and prevent or reduce the consequences of failures. The second is to avoid the consequences of failure. Sometimes, although a potential failure is detected, it cannot actually prevent it from failing, but it can still avoid or reduce the consequences of the failure. 
It turns out that a potential failure is an identifiable actual state that shows the process in which a functional failure is going to happen or is happening. Usually potential failures can be detected by the following means:
Condition Monitoring - Condition monitoring is nothing more than a more sensitive form of human senses, which is the use of special equipment to monitor the status of other equipment. The sensitivity of some monitoring devices is now very high. It can detect potential failure points and issue warnings of failure in advance several months. However, almost all condition monitoring devices have one of the biggest limitations is that they can only monitor one state, and The price of different condition monitoring systems varies greatly. There are also obvious differences in the requirements for use. Some monitoring devices require only skilled workers to operate, while others require very skilled technicians to operate. 
The detection of the main parameters - the main parameters of the equipment (temperature, pressure, flow, speed, level, etc.) are another kind of information flow of the equipment state. Compare the records of these information streams and their variants with the reference information. You can find signs of potential failure. However, the staff must know what the meter reading is in the normal state, what kind of reading corresponds to the potential failure, what kind of reading corresponds to the function failure, and the meter itself must be maintained to ensure that it has sufficient accuracy. 
The human senses - the most familiar condition detection technology is based on the senses of the person (see, hear, touch and smell). The use of senses to detect potential failures has the following advantages: First, people are pluripotent and can detect a wide variety of failure states, and any state detection technique can only be used to detect a potential failure; second, if it must be used People who perform normal duties near the equipment or near the equipment detect the failure. The economics of this type of inspection will be very high. 
In fact, it is also a condition monitoring method such as checking all the warning lights on the control panel, the operating status of the DCS card, and the inspection of the field devices every day. However, due to the increase of fault types and the complexity of fault manifestations, the traditional fault detection technology has become more and more powerless. Therefore, it is a work with broad prospects to make full use of modern technologies to detect potential faults. 
3.7 Using Derating Techniques to Increase System Safety Factor The use of derating techniques can further increase the reliability of components and systems. Derating can be achieved by reducing stress or increasing component strength. Experiments show that the failure rate of most electronic components changes with changes in temperature and electrical stress, and the higher the applied temperature stress, the higher the component's failure efficiency. For example: a transistor with a rating of 500 mW at 25°C, assuming it is used at two ambient stress levels of 55°C and stress ratios of 80% (400 mW) and 40% (200 mW), respectively At a stress ratio of 80% and a temperature of 55°C, the failure rate is 0.033x10-6. However, if the transistor is only applied with 40% stress at 55°C, the failure rate will drop to 0.010x10-6 and the reliability will increase by 2.3 times. Also, the resistor's withstand power cannot operate at its rated power, but should operate within 0.5 to 0.7 times its rated value. However, the derating design cannot be too low to allow reliable components to work effectively. The best derating should be at or below some point in the stress and temperature curve. At this point, we can look at With a slight increase in temperature or stress, the failure rate increases rapidly. Similarly, DCS highways, DPUs, and related cards should also strictly control their load rates. Otherwise, once an abnormal status is encountered, the sudden increase in the amount of information that needs to be processed causes information to be erroneous or blocked. 
3.8 Strictly enforce the rules and regulations
Currently implemented standards and procedures have sufficient efficiency. If they can be strictly enforced, then, if not all, at least the vast majority of accidents can be avoided. Therefore, for major equipment, especially protective components and equipment, periodic testing must be carried out according to the regulations, and equipment failures and test databases must be established. Compare the test data with the values ​​specified by standards and regulations, compare with the factory test data, compare with the previous test data, compare with the test data of similar equipment, and understand the trend of data change, and make a correct comprehensive analysis and judgment for the equipment. The transformation, adjustment and maintenance provide scientific basis. Analyze and count the equipment failures and defects recorded in the case to see whether the low quality of the equipment design or manufacturing is within a reasonable expectation range, and see if the number of such low quality occurrences is as large as possible. Poor design and process conclusions; - To eliminate the kind of misconception that compliance and enforcement standards and process systems are technically immature and timid. We must regard the implementation of standards and procedures as a necessary code of conduct for the completion of tasks, and we must also make every professional recognize that there are consequences of not implementing and complying with standards and regulations. 
3.9 Universal Reliability Knowledge and Analysis Methods Reliability technology is widely used in the analysis of electronic circuit and control system faults, but its application in the fault analysis of thermal power plant control systems is very limited. The main reason is the lack of professionals in this field. In fact, many common faults appear to be faults that often occur. If you let a technician who is familiar with reliability look at them, many of them are fatal potential faults. In addition, some unexplained failures use the Fault Tree Analysis (FAT) method in reliability technology to explore the causes of system failures and quickly identify those components that are the source of the failure. Second, if the failure rate of each component is known, the MTBF value of the system can also be calculated. The failure rate data of each component can be found in relevant reliability manuals and data. These data have great practical significance for system reliability analysis and calculation, component selection, and system maintenance decision. 
3.10 Strictly Controlling the Quality of Thermal Control Equipment
Maintenance activities may also reduce the inherent reliability of the system. Studies have shown that excessive reliability due to frequent maintenance repairs or poorly repaired repairs (such as assembly errors) can degrade system reliability. The development trend of system design is to reduce performance adjustment or continuous testing for acceptance. A large number of digital circuits are used instead of analog circuits, more in-house detection equipment and fault-tolerant circuits are used. These factors can greatly improve the ease of use (and can also increase the reliability of the system), thereby saving maintenance costs. Despite these measures, maintenance personnel are still the main reason for the decrease in reliability. Therefore, it is necessary to carefully evaluate and identify the impact on system reliability degradation that may be caused by those technicians with low technical level, poor treatment, or low rewards. At the same time, it is necessary to carefully evaluate the influence of the increase or change of hardware and software during the maintenance process. For the inspection and repair of important protection systems, the acceptance personnel shall personally see and personally inspect the maintenance process or the test progress to ensure that the repaired equipment not only recovers the design performance indicators, but also ensures that the repaired equipment can be operated reliably and stably. 
3.11 Improve the ability of operators to cope with emergencies
The production process that humans engage in involves the process of using energy to perform work. Once the energy is out of control, it may cause safety and environmental consequences. Therefore, there is inherent danger in the production process. However, the inherent dangers are all under the control of the human-machine environment. The accidents are often caused by the uncontrollability of human beings due to the uncontrolled behavior of the accident. The misoperation of the operators will cause the engineering design. The best intentions are lost. Practice has proved that the technical level, mental state, experience and maturity of the operator (operator reliability) have a very important influence on the safety of the production process. 
In the normal production process, the main task of the operator is to strictly observe the stable process and carefully supervise the working status of the automatic protection system and the standby status of the redundant standby system. When an abrupt change occurs in the production process and there is a possibility of a destructive accident, the operator should immediately take all the measures within his scope of responsibility and act quickly. The main thing here is that we must take error-free, correct actions. Error-free and correct actions have a lot to do with the length of service, technical proficiency, and age of the operators. Some people can control themselves and concentrate on critical situations, operate calmly and confidently, and use accurate and coordinated actions to eliminate failures and resolve accidents. Others lose faith, become panic-stricken, lose their souls, defy tactics, and eventually turn faults into accidents. Therefore, it is necessary to strengthen the training of operating personnel. This type of training includes two parts; one part is the basic theory and technical knowledge required for operation, and he enables the operator to have the analytical and logical capabilities for completing daily tasks. The other part is directly related to the need to personally operate the training, this part of the training should not be limited to normal operating procedures, but should pay attention to the system is not normal or the complexity of the situation should be anticipated when dealing with the limit, and finally pay attention to improve them The psychological quality enables them to face the crisis and meet their needs in the face of abnormal situations. 
4. Conclusion With the increasing scale of power generation equipment, higher requirements are placed on the safety, reliability and effectiveness of control systems. But no matter how advanced equipment, perfect design and clever control strategy, it is absolutely impossible to do it. From a reliability point of view, "faulty" is absolute, the problem is how the fault is caused, how to detect and discover potential faults as early as possible, then soften, control and eliminate faults, and reduce the consequences of faults. This requires the attention and support of leaders at all levels, as well as the concerted efforts and cooperation of all parties. The attention and support of the leaders can mobilize the enthusiasm and responsibility of the staff and improve the “response speed†to failures. The active cooperation of all parties can ensure that all necessary resources for troubleshooting are obtained before the failure occurs, and some unsafe hidden dangers can be accelerated. Elimination, shortening the time for troubleshooting or repairing faults, and abnormalities in operation and auxiliary engine failures, if operators can find, correctly judge, and promptly deal with them, they can also avoid the further expansion of abnormalities and faults, and can even save risks. . Therefore, in order to effectively reduce the protective action, we must strengthen the control over the quality of inspections and improve the quality of the inspection tour, so that equipment maintenance can often be run in accordance with the original design standards, and second, operators should be improved to deal with emergencies.
240 M3/h Concrete Batching Plants
During the maintenance of the mixing station, the main power supply must be cut off, the door of the distribution cabinet must be locked, and the key should be kept by the electrician.Power cutting and transmission must be operated by electrician.When starting the belt conveyor, mixing host, and other motors, it is necessary to observe whether there are people or other sundry things on the motor, in order to prevent injury or damage to the equipment when starting. When cleaning, it is strictly prohibited to flush the electric motor, electrical switch, solenoid valve and other electrical appliances with water to prevent electric shock and damage to electrical equipment.When the mixer is working, it is forbidden to stand in the discharging area.Non-operators are forbidden to enter the control room, smoking and doing things unrelated to the operation are prohibited.There is no operator in the operating room. Power must be cut off and doors and Windows must be locked before leaving.
Hzs Ready Mix Batching Plant,Hzs Mini Concrete Batching Plant,Hzs Batching Plant,Hzs Belt Conveyor Batching Plant
Shandong Zeyu Heavy Industry Science and Technology Co.,Ltd. , https://www.sdmobileconcretebatchingplant.com